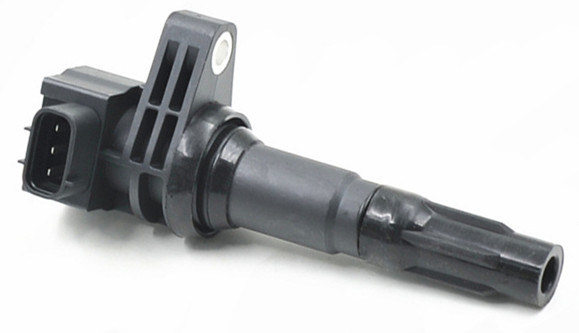
Typically, an ignition coil contains two sets of coils – a primary coil and a secondary coil. The primary coil uses thicker enameled wire, typically about 0.5-1 mm in diameter, wound around 200-500 turns; the secondary coil uses thinner enameled wire, typically about 0.1 mm in diameter, wound around 15,000-25,000 turns. One end of the primary coil is connected to the low-voltage power supply on the vehicle (+), and the other end is connected to a switch device (breaker). One end of the secondary coil is connected to the primary coil, and the other end is connected to the high-voltage output end to output high voltage.
The reason why the ignition coil can transform the low-voltage electricity from the vehicle into a high voltage is that it has a structure similar to an ordinary transformer, with a larger turn ratio between the primary coil and the secondary coil. However, the operation mode of the ignition coil is different from that of an ordinary transformer. An ordinary transformer operates at a fixed frequency of 50Hz, also known as a power frequency transformer, while the ignition coil works in a pulse mode, which can be regarded as a pulse transformer. It repeatedly stores and releases energy at different frequencies according to the different speeds of the engine.
When the primary coil is connected to the power source, a strong magnetic field is generated around it as the current increases, and the iron core stores the magnetic field energy. When the switch device disconnects the primary coil circuit, the magnetic field of the primary coil quickly decays, and the secondary coil will induce a very high voltage. The faster the magnetic field of the primary coil disappears, the larger the current at the instant when the current is disconnected, and the larger the turn ratio of the two coils, the higher the voltage induced by the secondary coil.
WeChat
Scan the QR Code with wechat